Introducción: En Importancia de Recognizing y Controlling Hilo Defectos
En el textil y ropa industria, incluso el smallest flaw en a coser hilo puede compromiso el calidad y durability de el final producto. En prendas a Inicio furnishings y industrial textiles, hilos son el connective tissue que holds el producto together. Poor-calidad hilos no sólo afectar a el appearance de costuras pero también plomo a breakages, unraveling, y cliente insatisfacción. That’s why comprender coser hilo defects y calidad control es esencial para manufacturers, calidad inspectors, y suppliers alike.
En Chino nacional estándar GB/T 6836-2007 offers a completo guideline para evaluating coser hilos, identificar common defectos, y defining acceptable calidad limits. Este artículo explora el major types de visual y structural defects found en coser hilos y how professionals puede inspect y prevent them. Through a detailed comprender de estos defects y control técnicas, businesses puede enhance producto coherencia, reducir returns, y build stronger marca credibility.
Calidad Control en Hilos Plays a Crucial Role en End-Producto Reliability
Calidad control en coser hilos goes beyond sólo reunión producto specifications—it garantiza cliente satisfacción, marca reputation, y long-term rendimiento. En manufacturing, hilos son sometido a altospeed costura, mecánico stress, environmental exposure, y blanqueo. A small inconsistency o imperfection en el hilo puede plomo a stitch fracaso, puckering, o breakage en tension.
Implementing rigorous coser hilo defects y calidad control procedimientos garantiza que hilos conozca defined rendimiento normas para tracción fuerza, color solidez, uniformity, y finish. Calidad control ayuda a detectar y isolate defective spools antes de ellos reach el producción floor, saving time, costs, y resources. Furthermore, it es vital para reunión internacional conformidad normas, including ISO, OEKO-TEX, y GB/T 6836-2007.
Visual Defectos Defined en GB/T 6836: What a Look For
GB/T 6836-2007 classifies several types de visible defects que compromiso el estética y funcional value de coser threads. Estos defects son typically inspected en adecuada iluminación y magnification, y ellos son grouped en categories tal como color inconsistencies, irregular surfaces, y físico flaws.
En más frequently encountered defects include:
-
Uneven hilo thickness
-
Loops o slubs
-
Frayed fibers
-
Foreign materiales stuck a el hilo
-
Lack de uniforme winding
Según a coser hilo defects y calidad control normas, visual inspección es el first y más crítico línea de defense. Inspectores son trained a detectar incluso subtle anomalies que mayo indique deeper problems en girando, teñido, o acabado procesos. Defective hilo appearance no sólo lowers producto appeal pero puede también afectar a costura calidad y fuerza.
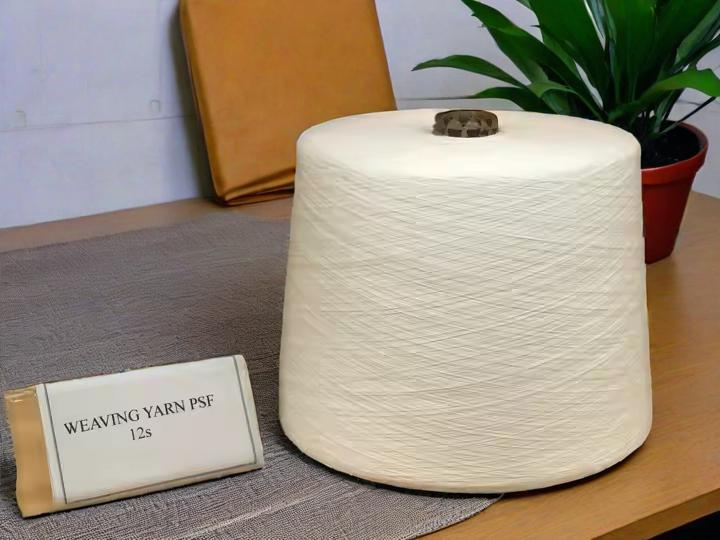
Hilados 40s 100% Poliéster
Common Hilo Defects: Knots, Color Difference, Shadow Core, y Stains
Among el más significativo defects en coser hilo defects y calidad control son knots, color variation, shadow core, y stains. Cada de estos presents único challenges en ambos producción y producto usage:
Knots: En some nudos son inevitable en hilo sinuoso, excessive nudos son unacceptable en altocalidad hilo. Knots puede causa aguja jamming, costura irregularity, y visual inconsistency en finished goods. GB/T 6836-2007 specifies allowable knot frequency para different hilo grades.
Color Difference: Inconsistent teñido puede resultado en visible shade differences along el same hilo spool o between spools en el same batch. Este es especialmente problematic para visible costuras en moda o decorative applications. Color variación a menudo stems from pobre dye bath control o desigual drying.
Shadow Núcleo: Este defect appears como a darker central línea within el hilo y es a menudo due a desigual dye penetration o twisting inconsistencies. En se convierte en noticeable en transparent o light-colored fabrics y puede alter el visual calidad de el seam.
Stains y Foreign Matter: Oil, dust, o química residue puede stain el hilo durante fabricación o handling. Not sólo do stains afectar a el appearance de el thread, pero ellos puede también plomo a discoloration de el cosido material.
Por identificar y clasificación estos cuestiones correctamente, fabricantes puede take corrective actions y prevent recurrence. Estos visible flaws son central a comprender coser hilo defects y calidad control at el operational level.
Acceptable Defect Limits Según a Hilo Grades
GB/T 6836-2007 categorizes coser hilos en different calidad grades, cada con su own permissible limits para various defectos. En three main calidad levels—Superior Grade, First Grade, y Qualified Grade—cada permitir a específico number de defects tal como knots, thick/thin spots, y color discrepancies within a estándar hilo length.
For example, Superior Grado hilos debe have mínimo visual defectos, low knot frequency (a menudo no more than un por 1000 meters), y no extranjero contamination. First Grado mayo permit slightly more variance pero still maintains tight calidad control. Qualified Grado hilos conozca el basic normas necesario para general use pero son no suitable para altofin applications.
Comprender estos grading benchmarks es a core aspecto de coser hilo defects y calidad control. En permite fabricantes a allocate hilos appropriately across different producto categories y mantener consistent normas para específico markets o clients.
Professional Hilo Inspección Requires Systematic Techniques
Professional hilo inspección implica a combination de manual, mecánica, y visual techniques. En clave a effective inspección lies en estandarizado protocols, trained personnel, y reliable tools. Manual inspections debe sea conducted en daylight-equivalent iluminación utilizando hilo inspección boards, magnifiers, o inspección rollers.
Mechanical tools tal como hilo longitud counters, tensión meters, y UV light detectors puede identificar cuestiones invisible a el naked eye. Digital colorimeters son también usado a evaluar color uniformity precisely.
An esencial pieza de coser hilo defects y calidad control es recordkeeping. Cada spool o batch debe sea tagged con calidad inspección reports que document detected problemas, batch origins, y resolution steps. Este traceability no sólo facilitates internal audits pero también builds trust con clients y certifiers.
Preventive Measures para Hilo Defect Reduction en Manufacturing
Preventing hilo defects begins at el raw material selection stage y continúa through el entire fabricación proceso. Here son clave preventive strategies aligned con coser hilo defects y calidad control principles:
-
En bruto Material Control: Use altocalidad fibers que son clean, uniform, y chemically compatible con previsto dye tipos.
-
Process Monitoring: Maintain strict control en spinning parámetros, twist levels, y tensión settings a prevent desigual winding o shadow core formation.
-
Dyeing Control: Use precision-controlado dye baths y garantizar uniforme agitation, temperature, y pH levels a avoid color inconsistencies.
-
Finishing y Winding: Employ anti-static agents, consistent waxing, y dust-free environments a reducir contamination y friction-related defectos.
-
Storage Conditions: Store hilos en humidity-controlado areas a avoid mold, moisture-related stains, o fragilidad.
-
Training y SOPs: Ensure operators son trained en defect recognition y estándar operating procedures (SOPs) para handling, inspecting, y envasado threads.
Sewing Thread Defects And Quality Control FAQ
How can I identify sewing thread defects?
You can identify sewing thread defects by visually inspecting the thread for irregularities, testing its tensile strength, and checking for color fastness. Professional testing equipment can also provide detailed analysis.
What quality control methods are used for sewing threads?
Quality control methods for sewing threads include regular testing for tensile strength, elongation, abrasion resistance, and shrinkage. Visual inspections, sampling tests, and adherence to international standards like ISO and ASTM are also crucial.
Why is quality control important for sewing threads?
Quality control ensures that sewing threads meet required standards for strength, durability, and performance. This helps prevent thread breaks, ensures consistent stitching, and guarantees long-lasting results in all sewing applications.

sewing thread suppliers
En a competitivo textil market, masterización coser hilo defects y calidad control puede sea el difference between a successful producto línea y a costoso producción fracaso. En coser hilos formulario el foundation de structural y estética integrity en cosido goods, garantizando su calidad through rigorous inspections es vital.
GB/T 6836-2007 proporciona a clear framework para identificar y limiting defects tal como knots, color variation, stains, y structural inconsistencies. Por comprender estos classifications y limits, fabricantes puede align su producción y inspección processes con global calidad expectations.
Professional hilo inspección y prevention strategies no sólo reducir devuelve y enhance cliente satisfaction pero también position a marca como a reliable proveedor de altorendimiento threads. Through mejor material selection, process control, y staff training, muchos common defects puede sea eliminated antes de ellos reach el producción floor.
En conclusion, a robust coser hilo defects y calidad controlprogram es un investment en calidad, reputation, y long-term success. Manufacturers who implement estos prácticas puede expect more consistent output, happier clients, y a competitivo edge en ambos doméstico y internacional mercados.